Where the Felt Baseline Meets the Bottom Line
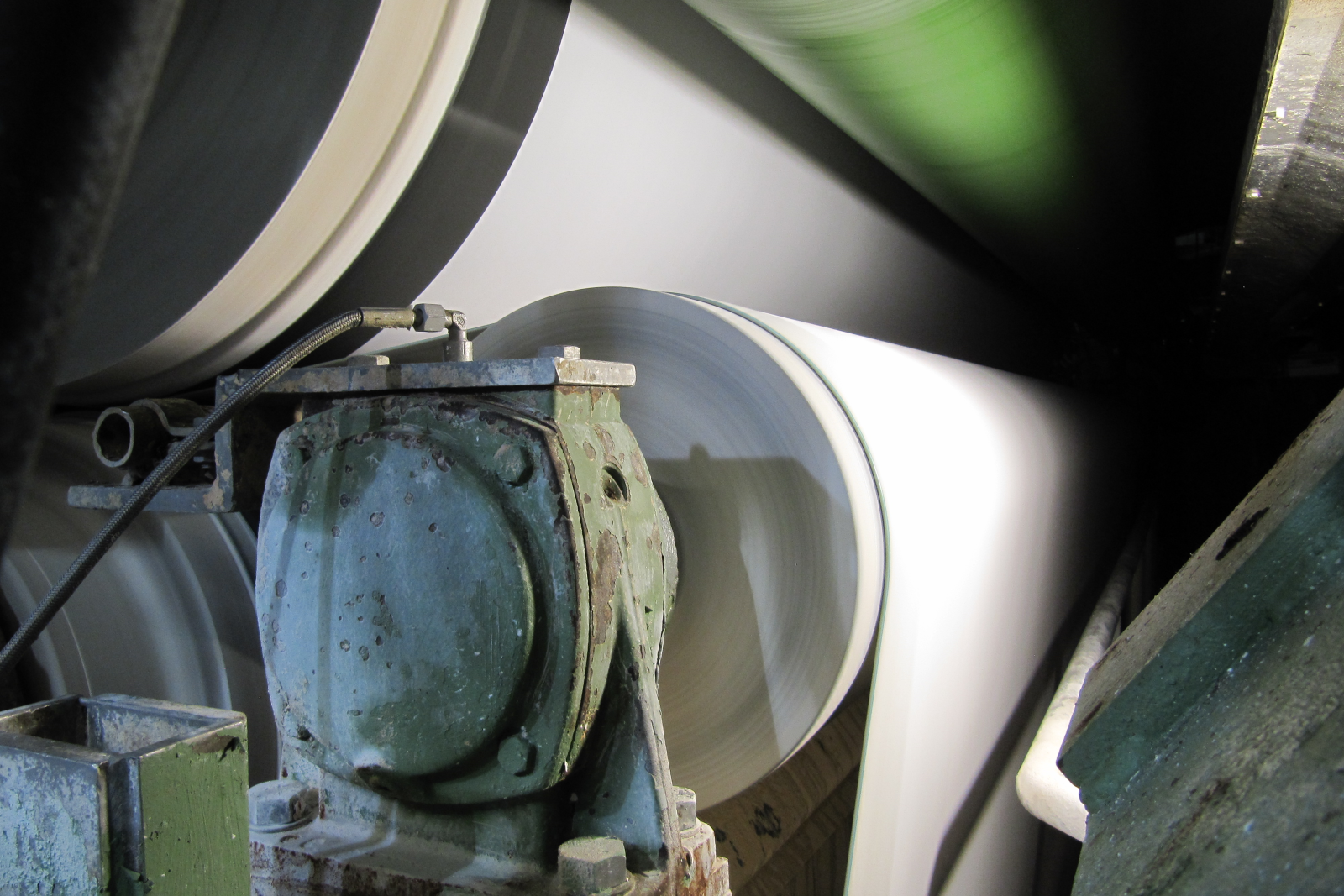
Do you make baselines based on days of felt life?
There comes a point in time when you start to wonder whether you are preaching to the converted. And for me, it’s the papermaking industry. At my company, Feltest, our mission is to promote knowledge sharing that benefits the papermaking sector as a whole.
Recently, we compared the results of another question held during a survey in our most recent and highly successful webinar, How to Assess Press Felts, to the results of the same question in a LinkedIn poll….Well, we ended up scratching our heads when we reviewed the results.
Mission accomplished? Really?
The results left us wondering, “At least for this topic, could it be that our mission is accomplished?”
Since I have my doubts about that, please allow me to explain. Then I will explain why this is so mission critical to our industry because a baseline means a better bottom line for papermakers.
Yes, if you create a baseline of a press felt position based on daily measurements, then you create the ideal conditions for your felt supplier to design new felts that could increase the sheet dryness after the press section by 1%. And 1% dryer out of the press section means 4% more output.
This percentage of output improvement almost doubles with each percentage point dryer out of the press section. The only investment you have to make is your own time and effort in performing daily measurements and creating a baseline. That’s it. It is really that simple. No CAPEX or major investment necessary.
The saga continues…
Now back to how we arrived here. In both our webinar and latest LinkedIn poll, we asked:
Do you make baselines based on days of felt life?
During the webinar, 15 out of 42 respondents answered “Yes” which is 44%. Out of 42 respondents, 6 answered, “I want to, but don’t know how to start” which totals 18%. The remaining 13 respondents amounted to 38% who all answered “No”. This means half of the respondents needed help getting started with their baselines.
After the webinar, and the subsequent distribution of the accompanying whitepaper How to Assess Press Felts: The basics for continuous felt improvement, we asked the same question in a LinkedIn poll. Unfortunately, despite having over 1,700 views, only 11 respondents participated.
From those 11 respondents, 82% answered “Yes”, 9% answered “No”, and the remaining 9% answered “I want to, but don’t know how to start”. But does this mean we have nearly reached everyone we can?
Feltest continues its mission of knowledge sharing
No matter which category of respondent you fall into, the purpose of this blog is to reach all of you. I will explain how you can encourage your suppliers to improve your felts by creating a baseline yourself. Ultimately, this will have a positive effect on your bottom line by enabling you to increase production.
1. Start with the daily data you already have
To start, better felts can do a lot for your machine output. Probably the best way to produce more tons of paper without an investment or CAPEX is to start optimizing your press felts. The first step is something you already have: daily data from the machine.
2. Daily measurements of dynamic permeability and compaction
The next step is to monitor the dynamic permeability and compaction of the felts on a daily basis. You can’t leave this to a number of suppliers that come by once a week, or only when the machine is running bad. You really need daily data.
3. Organize your data and create your baseline
The third step is to organize all this data according to the days of felt life. Press felts are the big variables in your machine and using their age as the X-axis for your graphs promises many new insights and will make it easier to set good development targets.
What I consider very important is that these graphs, which are based on the felt life, should also be shared with your supplier. They are the felt experts, they can figure out what to do with a design, but they also need to be clear on the current situation and the goals you want them to achieve.
4. Run and monitor trial felts - every day
Finally, trial felts have to be run and have to be monitored on a daily basis. With the newly established baselines for that position, it is much easier to see where a trial felt is going and how it is performing compared to the standard felt.
5. The Baseline Meets the Bottom Line
With the baselines, you reduce the risks of trials because you can make a better prediction about where a felt will be going the next few days and how it will affect your productivity. Better understanding of trial felts will boost innovation and, sooner or later, will boost the output of the machine.
By simply applying these easy steps, you can improve your felts and ensure your sheet leaves the press section 1% dryer: 1% dryer out of the press section = 4% more output. Every percentage point dryer out of the press section corresponds with about double the amount of output, so 2% dryer equals 8% more output.
In below example you can see that around day 44 things start to get bad: daily production (bronze) is decreasing and the steam consumption (green) is rising. You can also see that the blue line, the dynamic felt permeability, starts rising around that day. This indicates felt wear, more rewetting at the nip exit and, apparently, reduced daily output.
How did you respond to the question Do you make baselines based on days of felt life?
Yes, I do = Take me to the next level!
Get inspired in our article How a mill took advantage of PMC trials.
I want to, but don’t know how = Feltest’s whitepaper will give you a head start!
Get it now and get inspired in our whitepaper How to assess press felts.
No, I don’t = Don’t wait any longer! There’s no easier way to increase output without a major investment.
Read how easy it is in Feltest’s article about improving felts.
Remember: Daily Data Powers Production.
It will really help you increase the output of your machine.
Marcel Lensvelt
Founder and CEO of Feltest