Best Practices for Paper Machine Dryer Sections
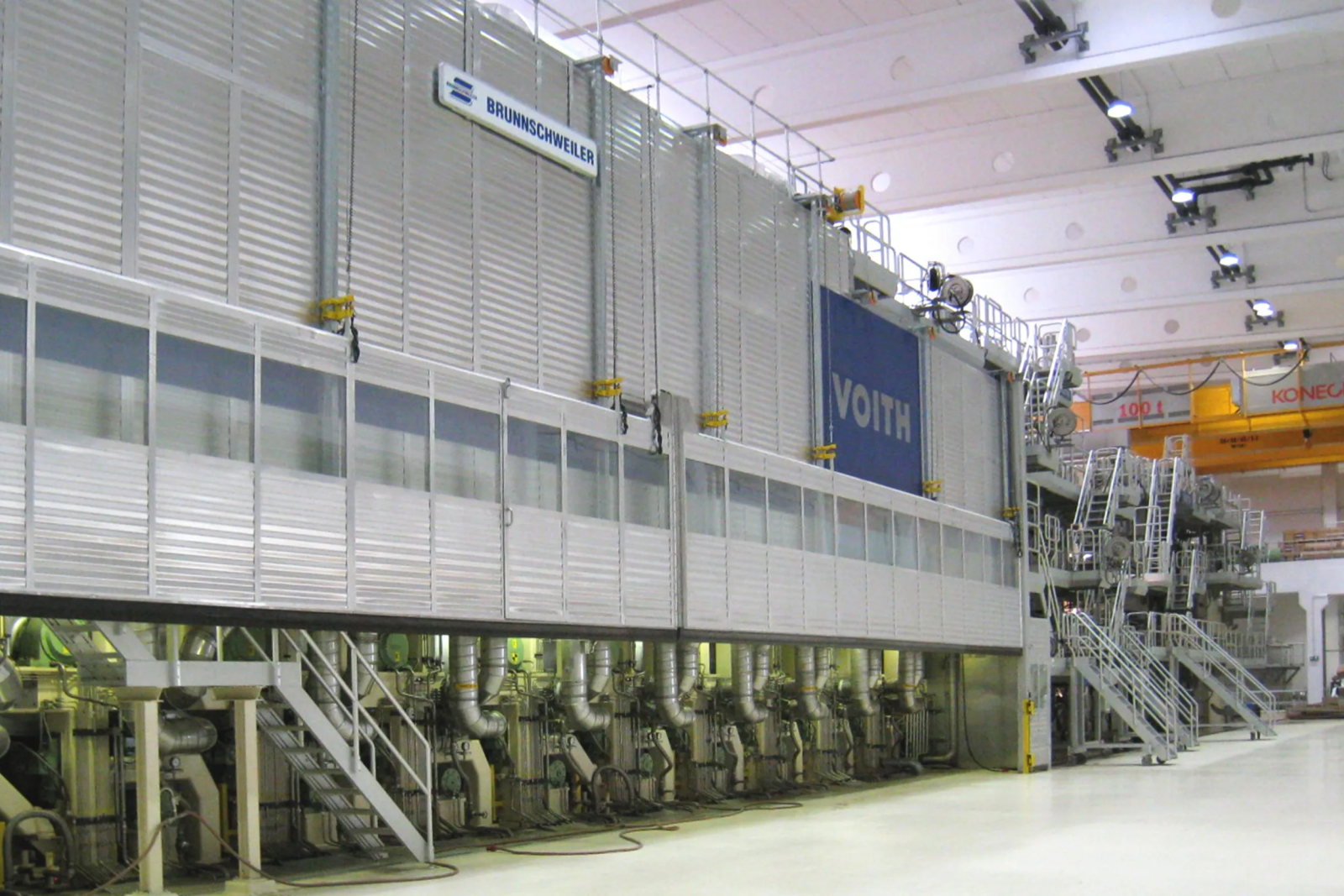
In the paper production process, the paper machine dryer section plays a crucial role in ensuring the final product meets the desired quality standards. Understanding the importance of this section and implementing optimization practices is essential for efficient operations and high-quality paper output.
In this blog, we'll explore the journey through the paper machine's dryer section, offering you the best practices for keeping things running smoothly.
Mastering Moisture
Despite its significance in papermaking, the drying process is relatively poorly understood and poses challenges due to its large equipment size and its high operational costs. The dryer section of a paper machine is responsible for removing a relatively small amount of water compared to the forming and press sections. However, it is considerably more costly to remove this water in the dryer section compared to other sections. The costs of dewatering are distributed as follows: forming section (10%), press section (12%), and dryer section (78%).
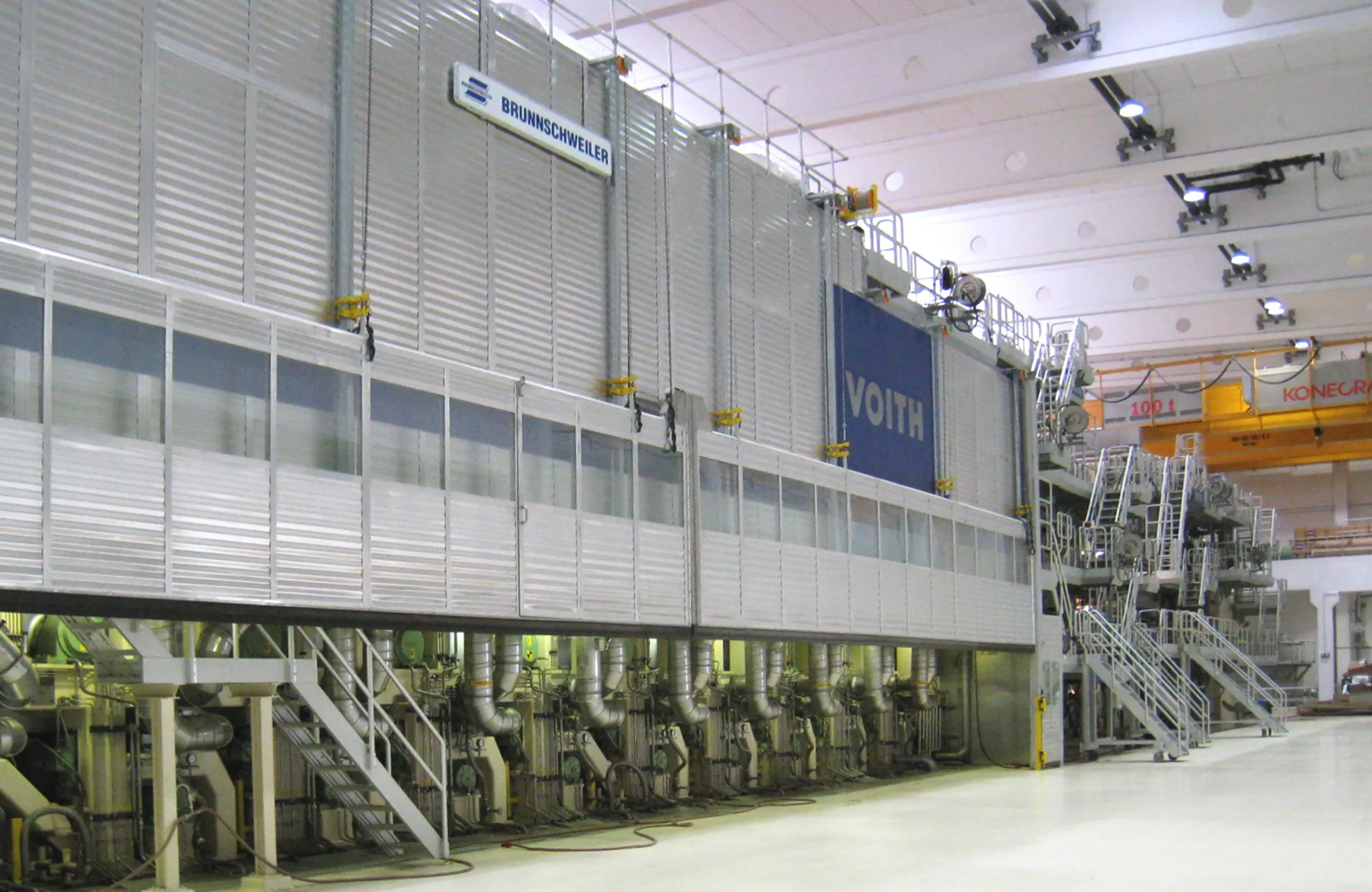
The dryer section also consumes a substantial amount of thermal energy in a paper machine and accounts for around 60% of the machine's total length (not including tissue machines) and nearly 40% of its capital cost.
Proper control of the dryer section is essential to achieve the desired paper properties. As the wet paper web enters the dryer section, steam-heated cylinders apply the heat needed to evaporate moisture. As the paper progresses through the dryer section, it loses remaining water, resulting in a dry and strong sheet.
Moreover, the dryer section also enhances paper surface properties. As moisture is removed, paper fibers align and compact, creating a smoother and more uniform surface. This improved smoothness not only elevates the paper's appearance but also enhances print quality. It allows for sharper and more vibrant prints, making the paper more visually appealing. Inadequate drying leads to issues like curling, blistering, and poor ink absorption. On the other hand, over-drying makes the paper brittle.
To create a balance between under- and over-drying, precise control of temperature, airflow, and moisture is essential to achieve optimal results and maintain paper quality.
Crucial Maintenance Practices for Dryer Sections
To keep the paper machine dryer section running smoothly and efficiently, you should follow these essential maintenance practices:
1: Regular Cleaning: Cleaning the dryer section removes accumulated debris and contaminants that can hinder drying. Dust and lint on cylinders, felts, and other components should be periodically cleaned using specialized equipment and cleaning agents.
2: Inspection: Regular inspection of cylinders, steam traps, and condensate systems is crucial to identify leaks or damage. Addressing these issues prevents energy waste and downtime.
3: Replacement of Worn-out Components: Worn-out dryer screens, seals, or steam joints can significantly impact drying efficiency. Regular inspections identify parts that need replacement, ensuring consistent performance and minimal paper defects.
4: Lubrication: Proper lubrication of bearings, gears, and moving parts reduces friction and extends equipment life. Establish a lubrication schedule and use appropriate lubricants to maintain optimal performance.
5: Monitoring Operating Parameters: Regularly monitor temperature, humidity, and airflow within the dryer section to ensure they remain within the specified range. Deviations can affect drying efficiency and paper quality, so maintain accurate and consistent operation.
6: Training and Education: Ensure maintenance personnel receive proper training to handle dryer section maintenance. They should be well-versed in safety procedures, equipment operation, and troubleshooting techniques.
In conclusion, adhering to these maintenance practices is essential for the efficient operation of paper machine dryer sections. By implementing these practices, paper manufacturers can maximize performance and equipment lifespan, leading to improved productivity and paper quality.
Techniques for Optimizing Dryer Sections
In addition to regular maintenance, consider these optimization techniques to enhance dryer section performance:
Adjusting Dryer Settings: Achieve optimal drying by monitoring and controlling parameters like temperature, humidity, and airflow within the dryer section. This ensures efficient drying without issues like over-drying.
Implementing Energy-Efficient Practices: Optimize energy use by employing heat recovery systems to reclaim energy from hot exhaust gases and preheat incoming process water. These practices reduce operating costs and support sustainability.
Utilizing Advanced Technology: Take advantage of real-time data monitoring and process control systems to accurately adjust dryer settings. Advanced dryer fabrics and coatings can improve heat transfer and enhance drying performance.
Troubleshooting Like a Pro
Despite proper maintenance and optimization, common issues can arise in the dryer section:
- Overheating: Prevent paper defects and reduced efficiency by monitoring temperature and adjusting steam pressure and dryer felt tension.
- Inconsistent Drying: Ensure uniform drying by addressing issues like improper airflow distribution, clogged steam pipes, or improper felt tension.
- Mechanical Failures: Prevent disruptions and impact on drying by conducting regular inspections, lubrication, and prompt repairs for mechanical issues.
By following these best practices and optimization techniques, paper manufacturers can maintain efficient operations, improve paper quality, and minimize downtime. This comprehensive approach supports the overall efficiency and profitability of the paper production process.